I just ran across some photos from my cell phone, and realized that I had never posted the results from this little project. I did buy a 1-3/4" Forstner bit, as I have several other uses for it.
The first pic shows my quick-and-dirty tube support ready for drilling. It's nothing but a couple scraps of construction lumber fastened together with decking screws, and it mounts to the Aux table with a couple of clamps. The hardwood scrap was clamped on just to back up the bearing block for through-drilling.
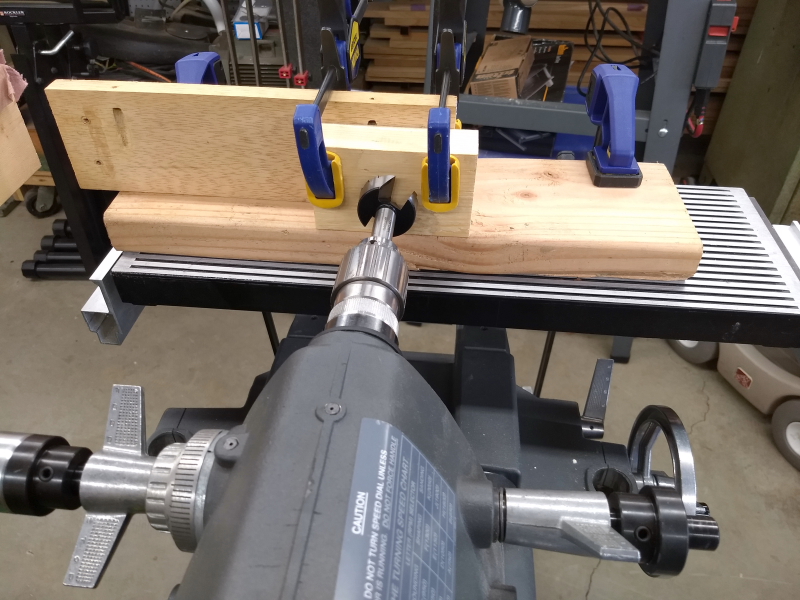
- Ready to drill.JPG (392.72 KiB) Viewed 11867 times
And now we have a nice clean hole. I applied some JPW to the ID as "sleeve bearing" lubrication.
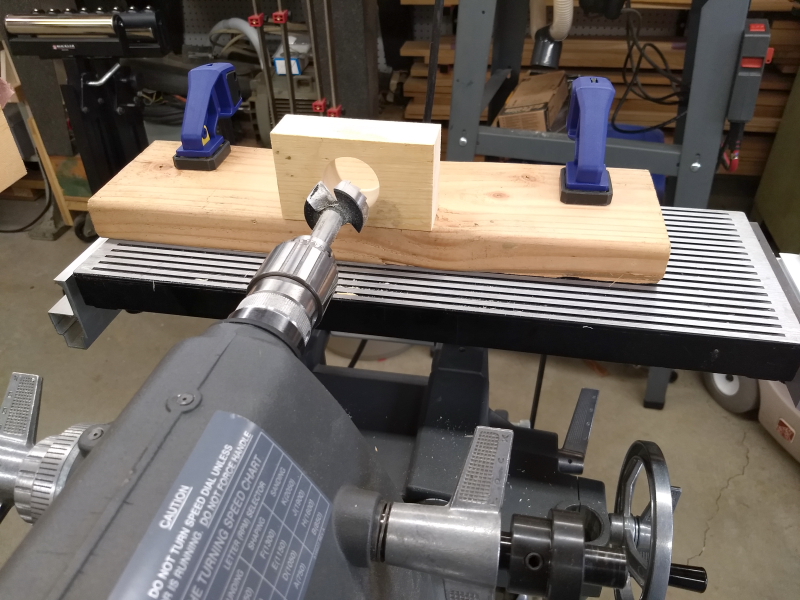
- Just drilled.JPG (395.56 KiB) Viewed 11867 times
In the pic below, the tube had just emerged from a good soak in a PVC pipe full of Evaporust. It slipped into the bearing bore easily, but with minimal slop.
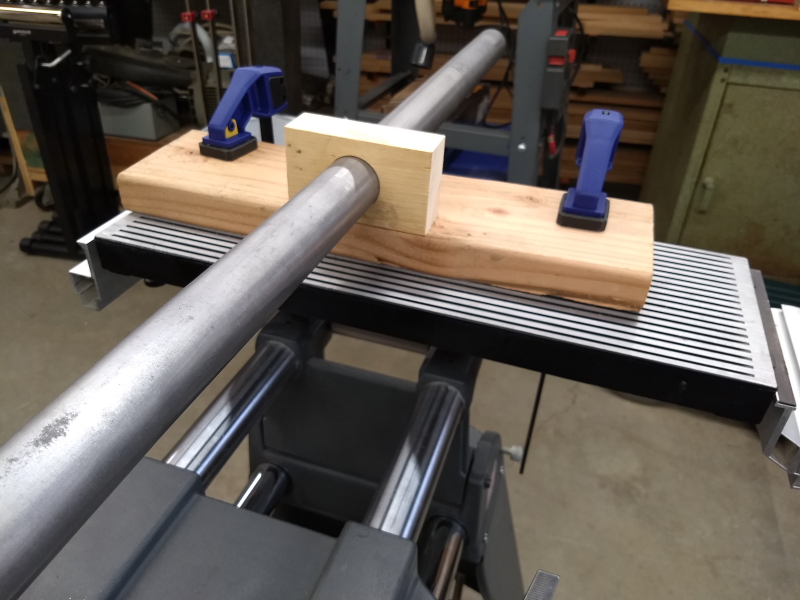
- De-rusted tube.JPG (334.07 KiB) Viewed 11867 times
Because I already had one, I used a rubber expansion plug to drive the tube. To get a better grip on it with the drill chuck, I replaced the hex nut with a longer hex standoff.
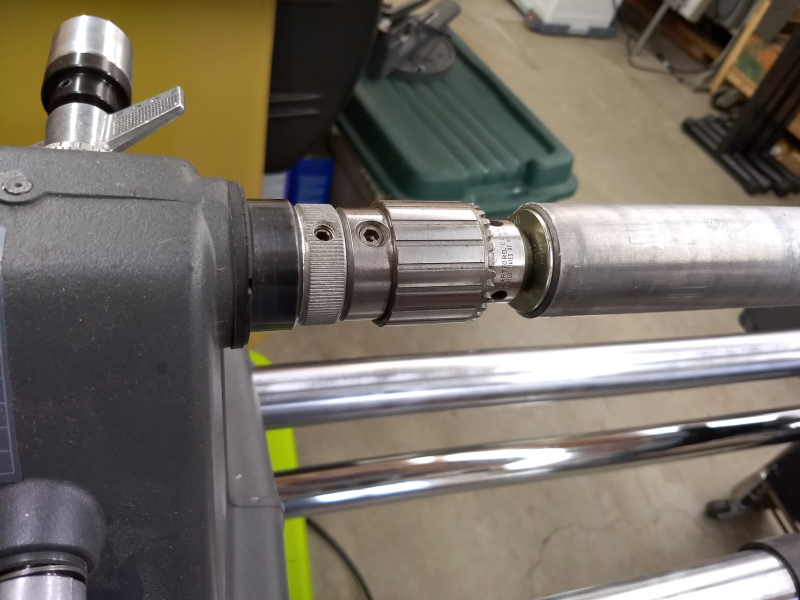
- Expansion plug.JPG (345.03 KiB) Viewed 11867 times
The "sleeve bearing" worked perfectly. After filing down the set-screw burrs, I cleaning the tube with 320-grit sandpaper, lubricated with mineral spirits. Because the "bearing" fully captures the tube, I was free to work from the front side of the machine, pressing the sandpaper upward against the bottom of the tube. Bearing friction was minimal, and the tube temperature rose only a little bit in the vicinity of the bearing. To access the part of the tube occluded by the bearing, I only had to extend the quill.
However, I realized that I should have relieved the bracket base back behind the bearing block. As pictured, the space between the tube and the bearing base is just the right size to suck in careless fingers. Needless to say, I sanded that little section of the tube from the top side, very very carefully.
Final polishing was done with a Nyalox brush in a cordless drill, with both the tube and the brush spinning. Here's a pic taken after polishing just the front tube.
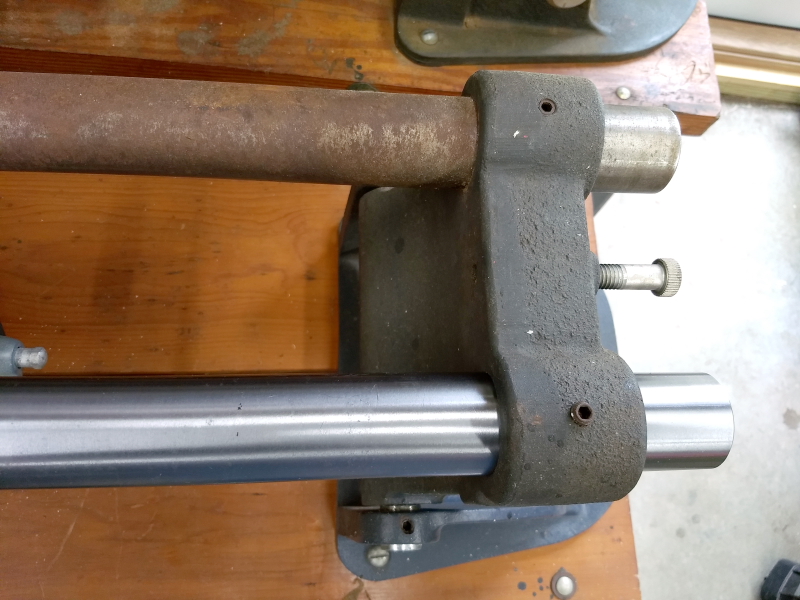
- Much better!.JPG (373.07 KiB) Viewed 11867 times